FSM and Predictive Maintenance in Support of the Golden Rule of Maintenance
- Published
- 6 min reading

What is the best way to maintain a number of devices, machines, and other equipment? Is the golden rule the answer to the needs of field service companies? And how can FSM and predictive maintenance help companies optimize their operations and costs? Discover how field service management software
Preventive Mmaintenance: what do we measure and why?
Mean time to failure (MTTF) andor mean time between failures (MTBF) are indicators which that dominate the perspective of any mature approach to device and/or machine maintenance. Apart from these indicators, we can distinguish others, which also refer to maintenance processes or organization processes. These include:
- Mean time to repair
- Time of request processing
- Work orders completed to schedule
- Work order ratio (planned vs unplanned activities)
- Work order backlog
- Tool time, which measures the utilization of resources
- Inventory/stock value
- Inventory turnover, which shows the movement of parts
- Delayed work
Other indicators refer directly to the outcome of the applied strategy for keeping devices and /machines working at the desired level of performance. These include engineering downtime and failure frequency.
Depending on the equipment criticality and the cost of failure and repair, MTTF or any other indicator, can be easily translated to operational expenditures. In healthcare, the cost of maintenance of basic devices such as dialysis machines, hematology analyzers, and anesthesia machines differs depending on the maintenance policy. It can easily reach USD 10, 000 or more annually for each machine. The same situation can be observed in any other area, for example, elevators in high-rise buildings, where 20 to 30 elevators per 1, 000 break down each month.
In general, the cost of maintenance for anthe industry is from between 15% toand 60% of the value of the goods produced. The general total cost calculated annually is well known and reported by all companies, but it’s not easy to match the cost to each piece of equipment or maintenance level, and it can be difficult to make a wise decision about where this cost is reasonable.
Types and levels of maintenance
Some devices and equipment types require more effort in order to be maintained. Before the solution goes live, it might require design, assembly, or installation.
The utilization of each machine can also vary, depending on the type. A machine might have many parts with different specifications and supplier/ or OEM requirements, or it may contain very simple elements such as valves or lightbulbs, which are very often a matter of maintenance processes. What we need to understand, is that we can have different levels and approaches in to operations to keep machines and businesses running. Some of the most common include:
- Proactive maintenance is applied at the design and/ installation stages. The quality of this stage can have a heavy impact heavily on future operations and failure frequency.
- Reactive maintenance means that devices are repaired when they stop working correctly. It can also be known as “run to failure”, and is very common for lighting repairs and so on, which are managed as unplanned activities.
- Corrective maintenance refers to a process by which parts of devices are repaired or/andand/or exchanged when they have symptoms of not working correctly. It’s applied to avoid any breaks in operations and is performed mainly performed as a planned activity.
- Preventive maintenance quite commonly named referred to as “fixed interval maintenance,” are is the repair or asset replacement activities performed according to the standards or OEM instructions based on time or usage.
- Condition-based maintenance is a more advanced approach to maintenance, where some parameters, such as noise and vibrations, are measured, and the maintenance is performed when set thresholds are reached.
- Predictive maintenance is an extension of the CbM approach, where more information is gathered in order to make a decision about whether a device or part of it requires repair or swap, depending on historical data, system design, and the impact of device failure on the E2E processes in the system.
- Prescriptive maintenance extends any other approach, and provides the root causes of the problems, which allows the reason for issues in a device or connected devices to be addressed.
Additionally, maintenance approaches are supported with by IoT devices or sensors which that analyze parameters such as temperature, rotations, or anything else that can be measured. Devices which that are a subject to monitoring can also be represented in IT systems as digital twins. A digital twin represents logically the device/ or system and collects data from the real devices. It allows simulations of machine lifespan, consideringthe lifespan of the machine, taking into consideration historical data about the device and other similar ones.
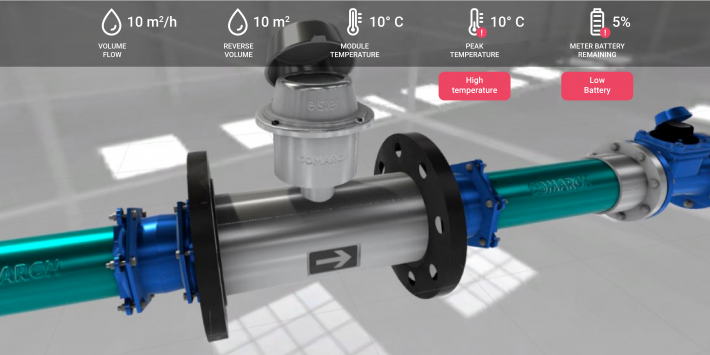
How it is all connected: the bathtub curve
Quite The complex modelling of different approaches to maintenance routines has its purpose. Various techniques can be applied at different stages of the device’s life, and can impact differently on operations and the the device’s health differently. This can be presented in a simplified manner on a “bathtub curve,”, which represents an analysis of failure frequency in the context of a machine’s lifespan.
At the early stage, named "infants mortality,", many problems are related to the quality of the installation. A proactive approach involving the right preparation of the project and the assignment of skilled engineers can shorten this period and lower the number of failures. Rapid corrective and reactive maintenance can also help.
In the "normal life" stage we use corrective and preventive maintenance to extend the life of the device and lower the number of failures.
When the equipment is used for a relatively long period of time, we need to rely on more sophisticated data from sensors, or simply pay attention to symptoms from first-level inspections, predict when an issue may arise, and work out the right time to replace the device.
The golden rule of maintenance
It looks like we have the remedy for all the problems in asset management and machine-based operations. In fact, we don’t. Each approach often requires dedicated IT tools, additional hardware sensors, and professional services to set up sophisticated systems for data analysis. It also calls for dedicated teams skilled in performing engineering operations the right way. And all of that results in costs.
The golden rule of maintenance, which is also used to decide which approach is valid for any device is:
cost of maintenance < cost of failure
Predictive maintenance, which requires more tools, has already been validated by its early adopters, and it gives value. In certain businesses, it also has a positive impact on maintenance costs. The hHealthcare is one example, where predictive/ preventive maintenance means that machines can be maintained three times cheaper than by adopting a reactive approach. Unfortunately, not all operations can build their own laboratories and set up CMMS, FSM, IoT platforms, and big data solutions. The golden rule will be broken.
A unified approach
It is clear that everything here is connected. We need to rely on the history of the device from its set-up to the end of its lifecycle. Furthermore, we can see that a unified environment that connects all KPIs and supports all techniques of maintenance is key. From work order management to scheduling, asset management, IoT, and data analysis, all tools should work together seamlessly. A unified approach is the right one, and may be the only answer in terms of both cost and quality. It is essential to have in place a system in which all data about the device and operations are is available, and which one that facilitates a holistic approach to machine health.